Prototype Development for High Performance Car Parts
Different Kinds of Prototypes
It is vital to test and retest a design from concept to completion in order to produce the best possible high performance car parts. Nothing in this world was ever perfect from the get-go, thus it is important to ensure that flaws and shortcomings are corrected before mass production can begin – especially when human lives are at risk.
The development of high performance car parts requires a different prototype in each stage of this process to check the manufacturability, overall safety and performance of the part. These prototypes are:
Design Prototypes
The first step in the development process is to have a plausible design to work on. These designs are usually created in a virtual environment and are represented by a volumetric solid model to test accuracy and reliability in a physical form. Assessing a physical prototype of the design enables the designer and manufacturer to identify any mistakes in the early stages of development.
Production Testing Prototypes
This prototype is more advanced than the previous one as it is made from the same material as the final product will be, whereas the design prototype is usually made out of plastic or more cost-effective materials. This prototype aims to assess if the car part can be machined and whether its geometry can be changed to decrease the amount of machining or not.
Client Testing Prototypes
The main purpose of creating this prototype is to test client or consumer satisfaction. The high performance car parts play important roles when manufacturing and selling a vehicle as a whole. It is crucial that the client or potential buyers are pleased with the prototype or else the final product will be a failure. Providing a testable prototype to those you are selling to will ensure that all parties are kept happy throughout the development process and the end-result is perfect.
Manufacturing Prototypes
The last and most expensive and time-consuming of all the prototypes is the manufacturing prototype. Created in the final stage of the development process, the manufacturing prototype will dictate whether or not your high performance car part is ready for mass production. Producing one successful part does not mean it can be replicated a thousand times over within an ideal timeframe and at peak condition. Manufacturing prototypes aid the estimation of time, efficiency and quality when producing the final product en masse.
Prototypes play an important role in the manufacturing of high performance car parts. They are a physical representation of the final product that saves time and money by revealing mistakes and inefficiencies before mass manufacturing. But how are these prototypes made?
Methods Used to Make a Prototype
Two popular methods used in creating prototypes for high performance car parts are rapid 3D printing and rapid CNC machining. As different prototypes are required at the various stages of the development process, it is recommended that both these methods be used as each one will provide a more accurate model of the design at any given time. Here, we take a brief look at the methods used in prototype creation but if you would like a more detailed discussion of these processes, we cover the topic in our blog: Methods of Creating Prototype for High Performance Car Parts.
Rapid 3d printing is a form of additive manufacturing whereby the final part mass is higher than that of the initial stock due to the adding of material rather than subtracting or rearranging it. The prototype is created through a process of fast fabrication using 3D computer-aided design (CAD). The end result is a scale model that closely matches the proposed finished product made in a cost-effective and efficient manner.
Where 3D printing is an additive manufacturing process, Computer Numerical Control (CNC) machining is subtractive. This method makes it possible to utilise computerised controls and machine tools to remove layers of material from a stock piece or blank workpiece to produce a custom-designed part. It is particularly useful in sectors where high accuracy is necessary, like in the automotive industry. This method of prototype development is also cost-effective and speedy while still delivering high-quality, defect-free car parts.
Prototype development plays an important role in the automotive manufacturing process and is a crucial step in producing high performance car parts of the best quality. Testing prototypes in various phases of the development process accelerates manufacturing and is a cost-effective practice that ensures an optimal final product.
Camtech offers prototype development services for the automotive industry, no matter how complex the process. Our complete integrated service covers design right through to high-end manufacturing. We provide high-precision performance engineering at its finest and pride ourselves with the latest technology and optimal production procedures. And as one of the UK’s leading and most innovative engineering businesses, our first-class reputation in the automotive arena and extensive expertise across numerous fields, including aerospace, means that our manufactured products are always at optimal performance, quality and safety.
Our experienced engineers work as a unified team to get your project complete, on budget and on time. And we have the proof to show for it. Products manufactured by Camtech have been used on many high-end marques including Porsche, McLaren, Aston Martin, Ferrari, Bentley, Bugatti, Subaru and more.
Get in touch to see how we can assist with all your prototype development needs.
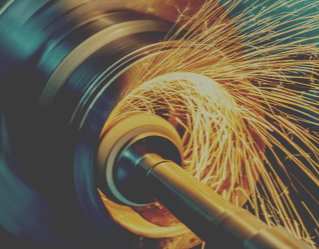